I begin with a favorite quote from a man I hugely respect.
When we want to excute a project we create a plan.
While you excute the plan things may not go according to the plan so we monitor the plan execution at reguar intervals.
Assuming something goes wrong during execution of the plan we should do 'Root Cause Analysis' to find
There are many diffrent techniques to conduct Root Cause Analysis. When I started working as a software engineer I was not familiar with tools and process to do Root Cause Analysis and I had to do study the resources on intenet to learn the various techniques. Later on when I started working for a MNC I had access to company's own customized training on Root Cause Analysis. The training was one fo the optional training, meaning it was not mandatory for all software developers and I had tried to convince our HR to make the training mandatory for all employees because problem solving is an essential skill and one should know about the ideal process and the tools available for Root Cause Analysis.
Anyway what surprises me is that even today when I meet some manager from diffrent industried I find many of them are not familiar with Root Cause Analysis (RCA) technique & tools. There are many different RCA techniques and you can follow any well defined technique. Manager should know that RCA is not some elite training and it is a essential skill. Unless every team member is trained to do Root Cause Analysis, the enterprise will not be able to know the real reasons for a problem, won't be able to fix problems or will take longer time to fix them and the impact to the enterprise is huge in terms of quality, efficiency and productivity.
Here is a self explanatory Root Cause Analysis excel template that you can customize or use it as it is.
(Link)
And here is a picture to summarize the Root Cause analysis process steps. there are many free trainings on RCA and I would recommend following the Sig Sigma DMAIC strategy for conducting Root Cause Analysis. DMAIC as you may be aware is acronym for five interconnected phases: Define, Measure, Analyze, Improve, and Control.
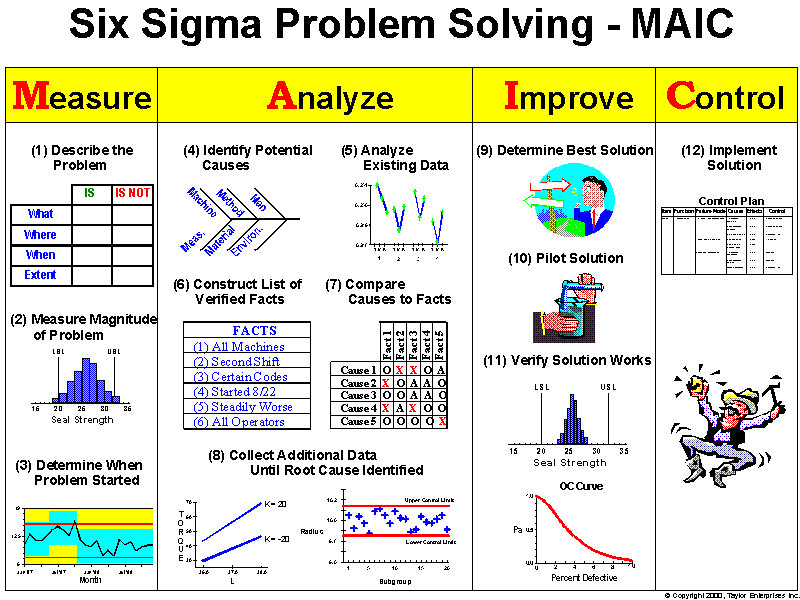
The above image is from Tayor Enterprise Inc
“Every defect is a treasure, if the company can uncover its cause
and work to prevent it across the corporation.”
– Kilchiro Toyoda, founder of Toyota
When we want to excute a project we create a plan.
While you excute the plan things may not go according to the plan so we monitor the plan execution at reguar intervals.
Assuming something goes wrong during execution of the plan we should do 'Root Cause Analysis' to find
- What is the problem & What is the frequency of occurance
- Why did problem occur or what is the trigger or cause of the problem
- When does the problem occur, is it a recurring problem
- How to fix the problem, What is the best solution
- How to improve existing processes to avoid reoccurance of the problem.
There are many diffrent techniques to conduct Root Cause Analysis. When I started working as a software engineer I was not familiar with tools and process to do Root Cause Analysis and I had to do study the resources on intenet to learn the various techniques. Later on when I started working for a MNC I had access to company's own customized training on Root Cause Analysis. The training was one fo the optional training, meaning it was not mandatory for all software developers and I had tried to convince our HR to make the training mandatory for all employees because problem solving is an essential skill and one should know about the ideal process and the tools available for Root Cause Analysis.
Anyway what surprises me is that even today when I meet some manager from diffrent industried I find many of them are not familiar with Root Cause Analysis (RCA) technique & tools. There are many different RCA techniques and you can follow any well defined technique. Manager should know that RCA is not some elite training and it is a essential skill. Unless every team member is trained to do Root Cause Analysis, the enterprise will not be able to know the real reasons for a problem, won't be able to fix problems or will take longer time to fix them and the impact to the enterprise is huge in terms of quality, efficiency and productivity.
Here is a self explanatory Root Cause Analysis excel template that you can customize or use it as it is.
(Link)
And here is a picture to summarize the Root Cause analysis process steps. there are many free trainings on RCA and I would recommend following the Sig Sigma DMAIC strategy for conducting Root Cause Analysis. DMAIC as you may be aware is acronym for five interconnected phases: Define, Measure, Analyze, Improve, and Control.
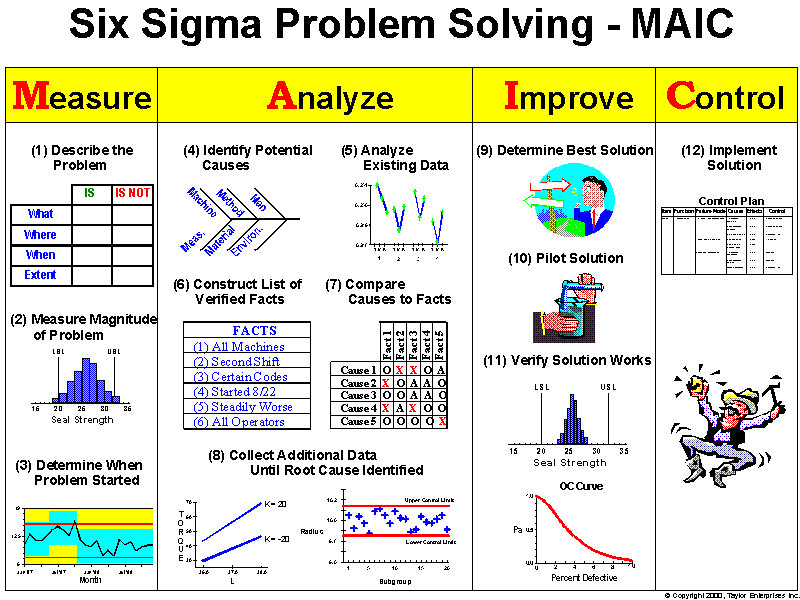
The above image is from Tayor Enterprise Inc
No comments:
Post a Comment